Можно собрать двигатель, который будет работать несколько месяцев, а можно выпускать такие, что клиент забудет про сервис на годы. Вот в чём разница между обычным производством и тем, где управление качеством — не просто слова для отчётов.
Сегодня каждый второй сбой детали на заводе — не случайность, а результат просчётов в процессе. Качество — это не только про визуальный осмотр на финальной стадии. Это ежедневная работа с материалами, чертежами, сборкой и даже обучением сотрудников. Управление качеством — штука, которая позволяет видеть брак ещё до того, как он превратится в проблему, и не тратить деньги на переделки.
- Что входит в понятие управления качеством
- Кто отвечает за качество на производстве
- Популярные инструменты и стандарты
- Как реально повысить качество продукции
Что входит в понятие управления качеством
Если коротко, управление качеством — это система, которая пронизывает все этапы: от проектирования детали до доставки финального продукта клиенту. Здесь нет места для случайностей или «авось пронесёт» — всё должно проходить по определённым правилам. Особенно это критично для машиностроения, где брак может не только стоить денег, но и обернуться рисками для людей.
В классическом понимании управление качеством включает четыре основных этапа:
- Планирование — заранее продумываются требования к будущей продукции и методы контроля.
- Контроль — постоянная проверка всех процессов (и не только в конце, когда всё уже собрано).
- Обеспечение качества — работы для предотвращения брака: всё от тестов сырья до анализа рабочих инструментов.
- Улучшение — выявление слабых мест и их постоянное устранение.
Простая схема, но количество нюансов в контроле качества зашкаливает. Например, в машиностроении применяют специальные измерительные машины, IT-системы для документации, а рабочие проходят регулярное обучение. Здесь не помогут хаотичные проверки: требуется чёткая последовательность и стандарты.
Вот небольшой пример реального подхода (по данным одного завода):
Этап процесса | Инструмент/метод контроля |
---|---|
Сварка корпуса | Автоматический ультразвуковой контроль каждого шва |
Поставка деталей | Лабораторная проверка металла на твердость и состав |
Сборка двигателя | Тестовые стенды для проверки под нагрузкой |
Круто, когда процессы выстроены так, что ошибка «вылетает» ещё на ранней стадии. Деньги на автоматизацию тратятся не зря — каждый выявленный дефект до клиентского этапа экономит бюджету приличную сумму.
Кто отвечает за качество на производстве
В машиностроении за управление качеством каждый отвечает по-своему. Ошибка думать, что только отдел контроля влияет на финальный результат. Фактически, цепочка начинается с инженеров и дизайнеров, а заканчивается рабочими на сборке и даже логистами.
Система такая:
- Инженеры и технологи: Здесь решают, какими будут допуски и из каких материалов всё делают. Ошибка на этом этапе напрямую даст брак на выходе.
- Производственный персонал: Рабочие должны строго выполнять инструкции и фиксировать любые отклонения. Тут сэкономить не получится — любые догадки заканчиваются повторными переделками.
- Служба ОТК: Классический контроль качества, но не единственный участник. ОТК берёт на себя финальную проверку и отбраковку.
- Руководство цехов и топ-менеджмент: Часто именно они принимают решения об изменениях процессов, внедрении новых стандартов или закупке нужного оборудования.
В реальных условиях хорошо работает схема, где ответственность поделена: каждый подписывает документ, подтверждающий контроль за своим этапом. На крупных предприятиях, вроде КамАЗа или ГАЗа, есть даже должность «ответственных по качеству» — их задача находить уязвимые места в любых процессах.
Вот простой пример цифрами: на одном крупном заводе внедрение системы всеобщего аудита качества (ежедневные мини-проверки каждым сотрудником) позволило снизить число возвратов продукции на 18% за год. Доказательство, что совместная ответственность работает лучше одиночных проверок.
Участник процесса | Роль в управлении качеством |
---|---|
Инженер | Выбор конструкций и материалов |
Рабочий на линии | Соблюдение технологий |
ОТК/Контролёр | Финальный контроль продукции |
Руководство | Обеспечение нужных условий и стандартов |
Когда все в цепочке в деле — качество продукции не становится случайностью. А значит, и клиенты возвращаются не с жалобами, а за новыми заказами.
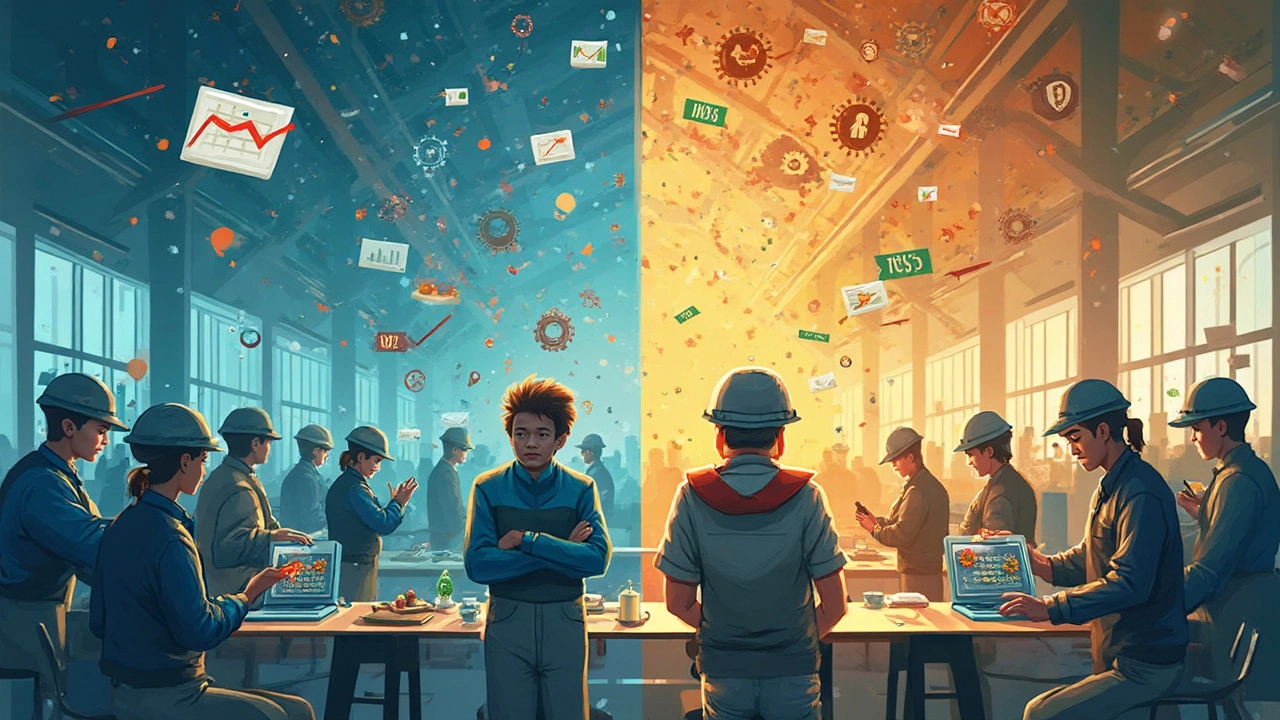
Популярные инструменты и стандарты
Без реальных инструментов управление качеством — просто слова. В машиностроении наибольшую роль играют стандарты ISO и проверенные методы контроля на каждом этапе. Давайте разберёмся, что рабочие действительно используют на практике, чтобы брак не попадал к заказчику.
Стандарт ISO 9001 — это, пожалуй, отправная точка. Сертификация по этому стандарту — не дань моде, а необходимость для выхода на серьёзный рынок. Требования прописаны максимально чётко: отслеживание процесса, контроль поступающих материалов, фиксация любой ошибки. По данным Ассоциации качества России, более 80% крупных заводов страны держат фокус именно на ISO 9001.
Вот какие инструменты чаще всего применяют:
- Контрольные карты — позволяют оперативно выявлять отклонения в размерах или свойствах деталей и сразу реагировать.
- FMEA (анализ видов и последствий отказов) — помогает рассчитать, где кроется главный риск и чего ждать, если не доработать процесс.
- Стандартизация рабочих инструкций — простыми словами, никто не делает на глазок, каждый знает свою технологию пошагово.
- Планирование контрольных точек — ещё до старта сборки прописывают моменты проверки: материалы, полуфабрикаты, готовые изделия.
Интересный факт: на заводах, где внедрены эти инструменты, доля возвратов по гарантии падает в 2–3 раза. А теперь немного фактов в цифрах:
Инструмент | Рост доли заводов с внедрением (с 2015 по 2023, %) |
---|---|
Стандарты ISO 9001 | с 55% до 82% |
FMEA | с 18% до 44% |
Контрольные карты | с 37% до 61% |
Каждый такой подход снижает риск поломки техники после продажи, а значит, экономит деньги и нервы. Современное управление качеством в машиностроение невозможно без инструментов и стандартизации, иначе одно и то же колесо будет собираться пятью способами — и один из них точно подведёт.
Как реально повысить качество продукции
Чтобы управление качеством в машиностроении стало не просто формальностью, важно внедрять на практике те методы, которые реально работают. Слепое копирование стандартов или покупка дорогих приборов не даст ощутимого эффекта, если не разобраться, зачем всё это нужно и как использовать каждый инструмент.
Вот базовые и продвинутые шаги, которые используют ведущие заводы в России и по всему миру:
- Стандартизация процессов. Без чётких инструкций на каждом рабочем месте каждый будет собирать по-своему. Фиксируйте все этапы, даже если кажется, что это мелочь.
- Внедрение системы раннего контроля. Контролируйте качество на входных этапах – сырьё, комплектующие, первые операции. По статистике, издержки на исправление брака на ранней стадии ниже в 7 раз, чем на финальной.
- Обучение персонала. Рабочие часто даже не знают, какой дефект критичен. Дайте примеры, проведите практические тренинги, а не просто раздайте список «что нельзя».
- Анализируйте причины брака. Обычное перекладывание вины между цехами не даст результатов. Используйте метод "пяти почему" или диаграмму Исикавы — эти штуки помогают быстро разложить проблему на составляющие.
- Отслеживайте статистику брака. Очень помогает простая таблица:
Месяц | Кол-во выпущенных изделий | Кол-во брака | Процент брака (%) |
---|---|---|---|
Январь | 5000 | 140 | 2,8 |
Февраль | 4800 | 96 | 2,0 |
Март | 5100 | 66 | 1,3 |
Часто после введения простого контроля с еженедельными разборками сотрудники сами начинают искать слабые места. Это не теория — так реально получилось сократить количество дефектных изделий на предприятии в Челябинске.
И ещё совет — не бойтесь внедрять элементы зарубежных стандартов, таких как ISO, даже если у вас маленькое производство. Проверенные мировые практики подкреплены цифрами, но применять их надо с учётом своей специфики, а не по шаблону.