Контроль качества часто воспринимают как скучную формальность, но расслабляться тут нельзя. В машиностроении любая пропущенная оплошность может стоить не только денег, но и репутации. Поэтому план управления качеством — не бюрократия для отчёта, а понятный инструмент, чтобы изделия не только выглядели хорошо на бумаге, но и надёжно работали в реальности.
Если коротко, план — это чёткая инструкция, что, когда и как проверять на каждом этапе: от закупки материалов до упаковки готовой детали. Без него в цехах начинается бардак: каждый сам себе инженер, нет гарантий, что завтра очередная партия не будет с браком.
На практике используют не один, а сразу несколько типов планов. У каждого свой фокус: где-то важно не пропустить дефектную партию сырья, а где-то — выстроить непрерывное улучшение после серии сбоев. Разобравшись в этих типах, можно экономить на издержках и не тратить время на бесконечные исправления.
Представьте — однажды известный производитель внедрил план контроля процессов не для галочки, а по уму. Результат? За год количество возвратов снизилось почти вдвое. А всё потому, что вовремя нашли узкие места в сборке и не ждали, когда клиент пожалуется.
- Что такое план управления качеством и зачем он нужен
- Тип 1: План инспекции и испытаний
- Тип 2: План контроля процессов
- Тип 3: План обеспечения соответствия стандартам
- Тип 4: План улучшения качества и работа над ошибками
Что такое план управления качеством и зачем он нужен
В машиностроении без плана управления качеством хоть куда — но не к стабильной продукции. Это документ, где расписано по шагам: что, как и когда проверяется, кто отвечает и на каком этапе. Его основная задача — чтобы не случилось сюрпризов типа «а почему детали не подошли?». Такой подход реально спасает от неразберихи и сбоев на производстве.
План помогает сразу всем: инженерам, контролёрам, менеджерам и даже клиентам. Когда все понимают, по каким правилам идёт работа, проще выявлять ошибки и оперативно их исправлять, а не ждут, пока клиент недоволен. Управление качеством — это не только про контроль, но и про экономию ресурсов: меньше некондиционных изделий, меньше возвратов и лишней переработки.
Вот какие вопросы решает план:
- Какие требования к материалам, комплектующим и сборке?
- На каких этапах и как проводится контроль качества?
- Кто отвечает за каждый вид проверки и кто решает, что делать при отклонениях?
- Какие документы подтверждают прохождение контроля?
Звучит просто, но если работать без конкретики, процесс быстро скатывается к хаосу. В России проведённое исследование среди 110 предприятий показало: у тех, где внедрён понятный план, число инцидентов с браком было ниже минимум на четверть. Это уже весомый аргумент не срезать углы на старте.
Чтобы план реально работал, важно держать его актуальным. Не бывает идеальной инструкции раз и навсегда. Новое оборудование, свежие стандарты, иной подход к обучению — гибкость только на пользу.
Кстати, работодатели всё чаще требуют опыт по работе именно с современными планами управления качеством. Не только «знать на бумаге», но уметь внедрять. И зарплаты у таких специалистов заметно выше.
Тип 1: План инспекции и испытаний
Этот тип плана — основа любого управления качеством в машиностроении. Если пропустить этап инспекции, можно легко получить серию деталей с одинаковым дефектом, а потом ломать голову, откуда взялась проблема.
План инспекции и испытаний — это чёткая таблица или схема, где расписано, какие проверки нужно делать, как часто, на каком участке производства и кто за это отвечает. Обычно документ выглядит примерно так:
Этап | Вид проверки | Ответственный | Частота |
---|---|---|---|
Входной контроль | Визуальный осмотр/Измерение | Техник по ОТК | Каждая партия |
Механическая обработка | Измерение размера/Жёсткости | Мастер участка | Выборочно, 1 из 10 |
Сборка | Функциональный тест | Контролёр ОТК | Каждый продукт |
Зачем нужна такая детализация? Например, по ГОСТу 16504-81 каждая операция по контролю и испытаниям должна быть зафиксирована. Это не просто требование закона — это гарантия, что случайности сведены к минимуму.
«Если нет чёткого плана по испытаниям, результат всегда рулетка», — так сказал Дмитрий Черненко, главный метролог одного из крупных заводов.
«Любая неучтённая мелочь — и серия уходит в помойку. Только строгий инспекционный план держит качество в узде».
В правильно составленном плане инспекции обязательно указывают:
- параметры, которые нужно проверять (размеры, прочность, наличие дефектов);
- методы проверки (например, ультразвук, штангенциркуль, визуальный осмотр);
- частоту выборки (каждая деталь, партия, случайный отбор);
- документы и протоколы для оформления результатов.
Внедряя такой план контроля качества, можно вовремя выявить и устранить проблему ещё на ранних этапах. По опыту многих инженеров, за счёт хорошо настроенной инспекции количество рекламаций сокращается на треть уже за первые полгода работы по чёткому плану.
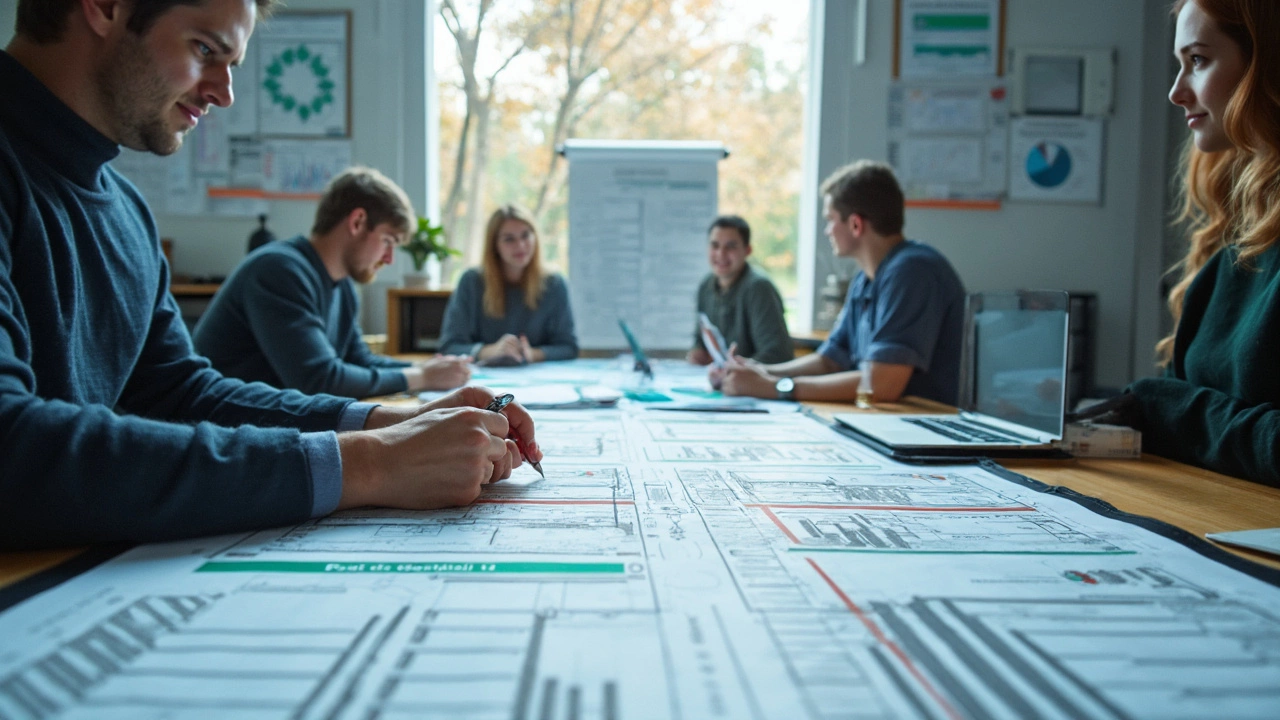
Тип 2: План контроля процессов
План контроля процессов ― это фактически «дорожная карта» для сотрудников, чтобы каждая технологическая операция шла по понятной и отлаженной схеме. Вот почему в машиностроении такие типы планов жизненно необходимы. Они не только снижают число случайных ошибок, но и стабилизируют качество в долгую — от тестовой партии до массового производства.
В чём суть? На каждом участке производства прописывают, по каким параметрам и с какой частотой ведётся проверка. Например, на сварочном участке могут контролировать толщину шва каждый час, а на линии сборки — момент затяжки болтов на каждой двадцатой детали. Так ошибки ловят на ранней стадии, не дожидаясь скандала с готовым изделием.
Характерный плюс такого плана — «прозрачность»: если возник сбой, легко найти, где именно он случился — не нужно гадать или устраивать расследования. Каждая операция фиксируется, по каждому сбою знают ответственного, а значит, и ответственность становится не теоретической, а вполне реальной.
Вот как обычно работает план контроля процессов в машиностроении:
- Определяют критичные точки процесса (например, измерение размеров после станка ЧПУ).
- Назначают сотрудников, кто отвечает за контроль на этих точках.
- Устанавливают частоту и методы измерений (ручные, автоматические, поэтапные выборки).
- Формируют таблицы с нормами: какой результат считается годным, а какой — уже поводом остановить линию.
- Регистрируют все данные в специальных журналах или в электронной системе.
Есть интересная статистика. На одном из автозаводов после внедрения прозрачного плана контроля процессов количество внештатных остановок упало с 12 случаев в месяц до 3 всего за полгода. Это обеспечило не только экономию времени, но и уверенность: клиент получит то, что заказал.
Этап производства | Что контролируется | Частота проверок |
---|---|---|
Механообработка | Геометрия деталей | Каждая десятая деталь |
Сварка | Качество шва | Ежечасно |
Покраска | Толщина покрытия | Каждая партия |
Если самому собирать план контроля процессов, не надо изобретать велосипед: начните с того, что реально влияет на качество, добавляйте только то, что проверяется на практике, а не на бумаге. Регулярно пересматривайте план — иначе он устареет и станет балластом.
Тип 3: План обеспечения соответствия стандартам
Вот здесь начинается самое интересное для управления качеством в машиностроении. Практически все заказчики ждут не только красивую бумажку по отгрузке, а реальное подтверждение: детали соответствуют ГОСТу, ISO или конкретным требованиям автопроизводителей. И если документы расходятся с фактом — начинается головная боль у всех.
План обеспечения соответствия стандартам — это чёткая инструкция, как доказывать, что каждая партия деталей действительно надёжна. В таких планах обычно указывается:
- какие именно стандарты или нормы применимы, например, ISO 9001, ГОСТ 2.601, DIN EN 10204;
- какие документы нужно собрать (сертификаты, отчёты лабораторий, протоколы испытаний);
- кто и в какие сроки отвечает за проверку и оформление документов;
- порядок валидации изменений — если, например, сырьё внезапно меняется.
Насчёт фактов: около 75% предприятий машиностроения в России ориентируются на международные стандарты ISO, чтобы быть конкурентоспособными за рубежом. Кстати, в 2023 году чаще всего нарушения находили в неправильном оформлении протоколов испытаний — и это банальные ошибки, которые просто не заметили на этапе подготовки документов.
Полезный совет — не храните контрольные процедуры только в голове старшего технолога. Заводите специальный реестр, где видны все этапы проверки, сканы сертификатов и номера протоколов. Хорошая электронная система позволит быстро найти нужный документ, если появится внеплановая проверка или спор с заказчиком.
Простой пример:
Стандарт | Документ | Ответственный | Срок проверки |
---|---|---|---|
ISO 9001 | Сертификат соответствия | Менеджер по качеству | 1 раз в год |
ГОСТ 2.601 | Протокол испытаний | Лаборант | На каждую партию |
DIN EN 10204 | Сертификат 3.1 | Заводской технолог | Перед отгрузкой |
Не старайтесь «догонять» стандарты только для галочки. Всё равно проверят на производстве или в поставке — и если обнаружат нарушение, возвраты, штрафы и скандалы обеспечены. Системный подход реально экономит время, деньги и нервы. Заведите список стандартов под каждый вид продукции — это снимет тысячу вопросов у менеджеров, тех, кто выпускает детали, и отдела продаж.
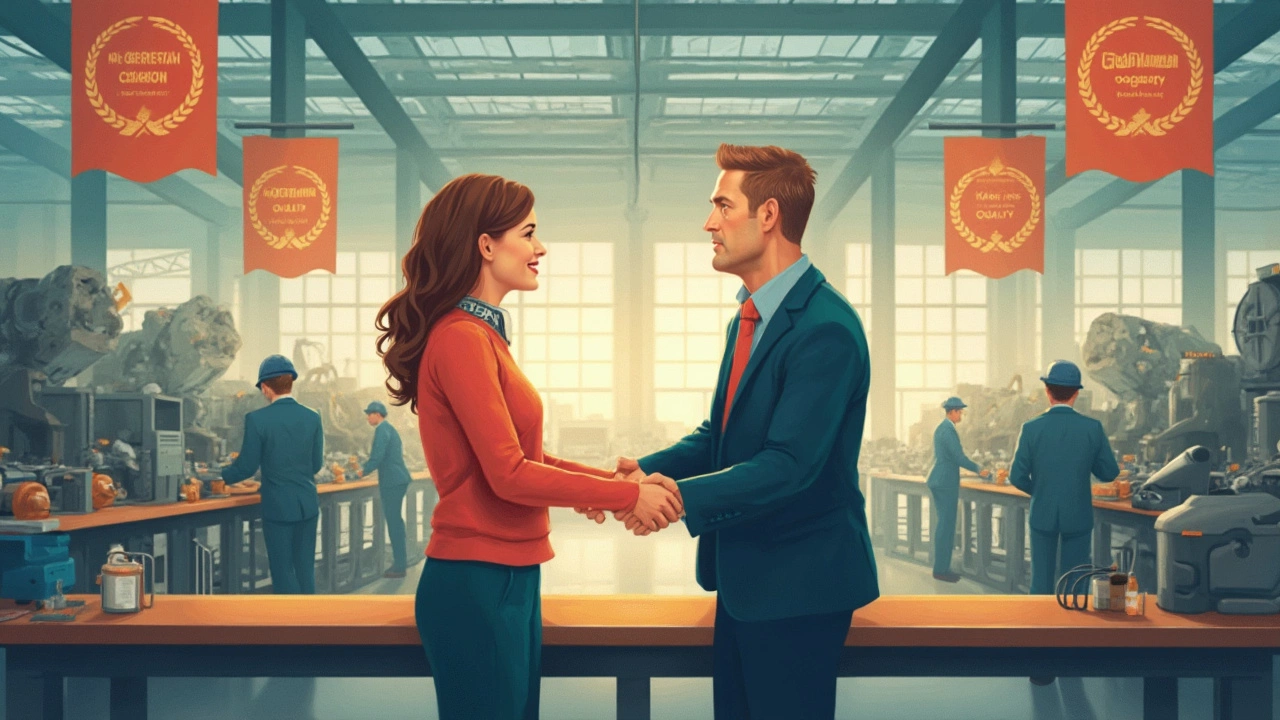
Тип 4: План улучшения качества и работа над ошибками
Вот где начинается настоящее управление качеством – не просто обнаружили ошибку и забыли, а выстроили систему, чтобы эта ошибка больше не повторялась. Хороший план улучшения качества – это не очередная таблица для отчёта, а конкретные шаги, которые реально работают на производстве.
Базовая идея простая: увидели косяк — разберись, почему он случился, внедри изменения, замерь эффект. Для этого нужны:
- чёткая фиксация всех случаев брака или отклонений;
- регулярный сбор отзывов от работников и клиентов;
- анализ причин с помощью простых инструментов (например, диаграммы Исикавы или «5 почему»);
- создание плана действий и назначение ответственных;
- проверка, как изменяются показатели после внедрения новых решений.
В машиностроении круто работает методика PDCA (Plan-Do-Check-Act, по-русски — «Планируй-Делай-Проверяй-Действуй»). Если внедрять такой цикл каждый месяц или квартал, уровень брака реально падает.
Посмотрите на эти цифры — данные открыты: на заводах, где после ошибок сразу запускали PDCA или Kaizen (маленькие ежедневные улучшения), средний процент брака со 2,4% снизился до 1,1% уже в первый год. Экономия на возвратах и ремонтах переваливает за миллионы рублей, особенно на крупных предприятиях.
Показатель | До внедрения плана | Через год |
---|---|---|
Процент брака | 2,4% | 1,1% |
Количество возвратов | 870 | 370 |
Чтобы такой план управления качеством не завис в бумагах, держите его простым и конкретным. Не бойтесь ошибаться, бойтесь ничего не менять. Пусть каждый сотрудник знает: если что-то пошло не так — не замалчиваем, а сразу включаемся в исправление и улучшение процесса.