Может показаться, что контроль качества — это скучная бумажная рутина где-то на заводе. На самом деле без него весь процесс машиностроения просто рассыплется, как пазл из дешевого пластика. Одна просроченная деталь — и потом весь цех стоит, а начальство пишет объяснительные.
В машиностроении контроль качества — будто система безопасности для всей продукции. Нет разницы, делаете ли вы гигантские станки или крепёж: если детали разбегаются по размерам, в итоге ничего не соберёшь. Отсюда и постоянные проверки: забраковать ненадёжное, не пропустить битое сырьё, вовремя заметить сбои.
Просто так проверять ради галочки никто не станет — на какой-то стадии контроля всегда можно спасти ситуацию. Например, если ошибка найдена рано, переделка обойдётся дешевле. Если же брак всплыл в финале или, чего хуже, на стороне заказчика — урон по кошельку и репутации будет куда сильнее. Часто из-за одного пропущенного дефекта возникают аварии, срывы контрактов и разборки на самом высоком уровне.
- Зачем вообще нужен контроль качества в машиностроении
- Основные виды контроля качества: просто и понятно
- Входной контроль: фильтруем сырье
- Операционный контроль: ловим ошибки на этапе производства
- Приемочный контроль: финальная точка
- Советы и лайфхаки: что работает на практике
Зачем вообще нужен контроль качества в машиностроении
Без контроля качества ни одно машиностроительное предприятие не выживет. Если полагаться только на удачу, линия быстро встанет: детали не подойдут друг к другу, станки сломаются, заказчики будут устраивать скандалы из-за брака. На кону не только деньги — огромные штрафы и даже судебные иски не редкость, когда речь о крупных производителях.
По статистике, если снизить брошенный дефект всего на 1% на этапе сборки, то потери компании уменьшаются на десятки миллионов рублей в год. Особенно это актуально для тяжёлого машиностроения, где из-за одной бракованной заготовки можно задержать весь проект недели на две. Такие случаи — не редкость.
Контроль качества в машиностроении решает сразу несколько важных задач:
- Гарантирует соответствие продукции стандартам ГОСТ, ТУ и чертежам.
- Снижает издержки за счёт быстрого выявления дефектов.
- Защищает репутацию завода — довольный клиент возвращается вновь.
- Позволяет экономить: брак на ранних стадиях исправлять дешевле всего.
- Обеспечивает безопасность — в машиностроении ошибки часто приводят к авариям и травмам.
С каждым годом требования к управлению качеством только растут: клиенты хотят не "просто нормально", а идеально. Инспекции стали жёстче, контролируют не только сами детали, но и документацию, условия хранения, работу оборудования.
На практике хороший контроль — это не формальность, а реальный инструмент экономии и выживания на рынке. Руководители давно поняли: проще вложиться в проверки, чем потом разбираться с рекламациями и потерями.
Стадия | Стоимость исправления брака, % от цены изделия |
---|---|
Входной контроль | 1-5% |
Операционный контроль | 5-20% |
Приемочный контроль | 20-100% |
Чем раньше система контроля качества отсеет дефект, тем «дешевле» он обходится предприятию. Ждать финальной сборки — это всё равно что пытаться поймать комара уже в супе.
Основные виды контроля качества: просто и понятно
В машиностроении нельзя полагаться на авось. Тут контроль — не только требование ГОСТа, но реально нужная штука для спокойствия инженеров и технологов. Основные виды контроля качества легко уложить в четыре главные категории. Каждый из них решает свою задачу и страхует на разном этапе — здесь нет лишних и необязательных пунктов.
- Входной контроль. Первая линия обороны: проверяют материалы и комплектующие до запуска в производство. Задача — не пустить внутрь то, что потом испортит всю партию.
- Операционный или пооперационный контроль. Производство идёт, детали движутся по станкам — тут смотрят за процессом, ловят огрехи сразу, чтобы не делать брак дальше по цепочке.
- Приёмочный контроль. Финишная проверка — всё, что сделали, тестируют, сверяют с чертежами, проверяют работоспособность. Только после этого деталь уходит к заказчику.
- Периодический (или инспекционный) контроль. Его можно встретить не везде. Это, скажем так, плановая ревизия целых процессов, станков, условий труда. Обычно раз в квартал или по графику.
Эти методы комбинируют. Например, входной и пооперационный часто сливаются, когда сырьё поступает сразу на линию, а оператор тут же с калибром. Есть предприятия, где на приёмке сталкивают сразу несколько подходов: микроскоп плюс УЗИ-дефектоскоп и реальные испытания нагревом.
Для представления, насколько важна многослойность, взгляните на такую реальную схему с одного машиностроительного завода:
Вид контроля | Ответственные | Как часто проводится |
---|---|---|
Входной | Отдел контроля качества | На каждую партию |
Операционный | Мастер смены | На каждом ключевом этапе |
Приёмочный | Отдел приёмки | Финал производства |
Есть нюанс: любой вид контроля качества можно настроить по-разному под конкретный цех, оборудование, тип продукции. Современные системы иногда добавляют автоматическую проверку — датчики, лазеры, камеры, которые исключают человеческий фактор. Но ручной труд пока никто не отменял — особенно для сложных или штучных задач.
Входной контроль: фильтруем сырье
Без нормального контроля качества на входе вы рискуете сразу «влить» много денег в откровенно плохое сырьё. В реальном заводском цикле входной контроль — это первая линия обороны от брака. Проверяют всё, что поступает на склад: металл, пластик, электронные компоненты, инструмент.
Поставки сейчас часто идут от десятков разных фирм. Один недосмотр — партия с дефектом, которая, если не задержать на старте, потом просядет по всем этапам производства. Обычно нарекания вызывают кривые размеры, микротрещины, усталость материала, скрытая ржавчина, подделки по марке стали. Производитель прислал паспорт на металл? Отлично, но его данные всегда сверяют с реальными замерами.
- В лаборатории или на месте проводят быстрые анализы и тесты. Простые замеры — штангенциркулем, микрометром, ультразвуком (для металла).
- Если сырья много — берут пробы. Обычно это 2–5% от партии, но на особо ответственных деталях могут проверить всю поставку.
- Тестируют не только геометрию, но и свойства: твердость, химсостав, однородность.
Для отчётности все замеры сразу записывают в электронные журналы или указывают в маршрутных листах. Если где-то выявили косяки, всю поставку блокируют или возвращают на доработку поставщику — не жалуются, а действуют по регламенту.
Тип сырья | Частые дефекты | Инструмент проверки |
---|---|---|
Сталь рулонная | Трещины, несоответствие толщины | Микрометр, ультразвук |
Пластик | Включения, пузыри | Визуальный осмотр, микроскоп |
Электросхемы | Повреждённые дорожки | Мультиметр, лупа |
Здесь нет места компромиссам: все отклонения фиксируются и обсуждаются сразу, чтобы потом не было мучительно больно из-за повторяющихся браков. Система жесткая, но рабочая — без неё даже пройти первый этап по управлению качеством невозможно.
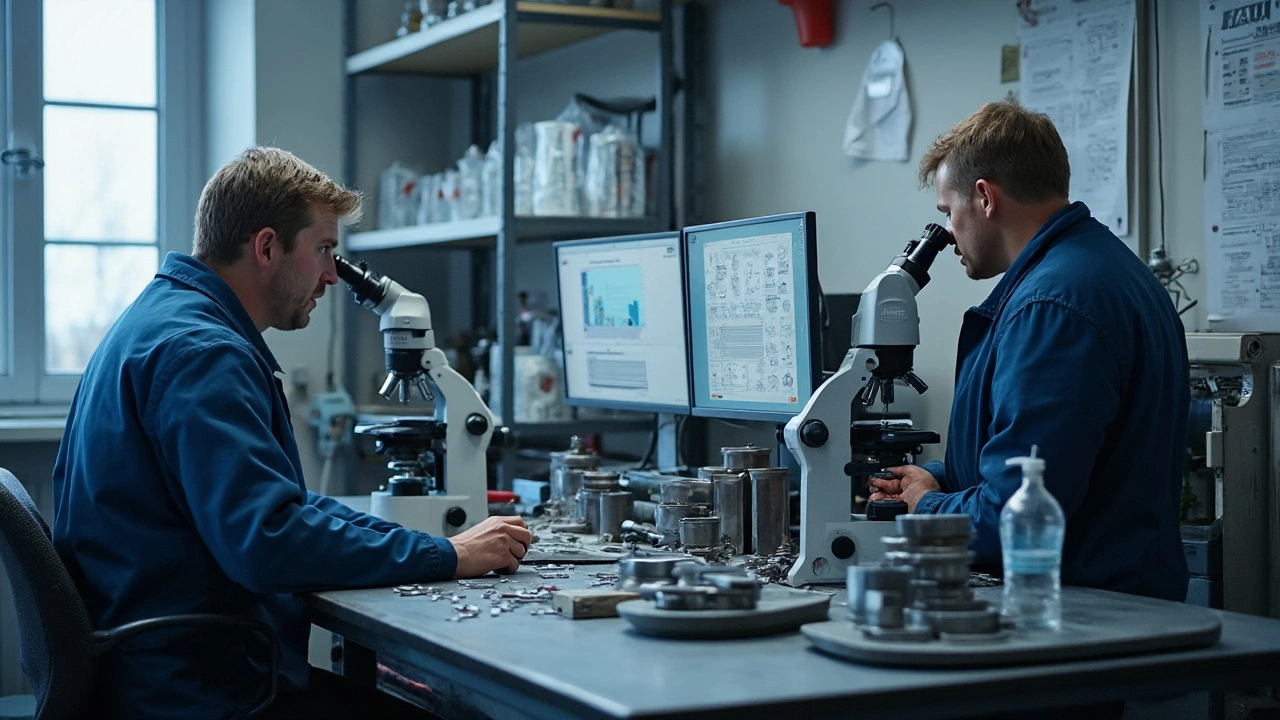
Операционный контроль: ловим ошибки на этапе производства
Когда в машиностроении говорят про контроль качества на производстве, чаще всего имеют в виду именно операционный контроль. Всё просто: смотрим за тем, чтобы каждая операция шла как надо — не после, а прямо во время работы. Тут сэкономленные минуты выливаются в спасённые тысячи рублей.
Операционный контроль внедряют на каждом ключевом этапе: подогнал токарь размер — проверь микрометром; сварщик собрал корпус — проконтролируй качество шва. Чем раньше найдёшь косяк, тем проще и дешевле его исправить, не дожидаясь, пока пол-линии из такого брака соберут.
Обычно на практике действуют так:
- Точность деталей замеряют после каждой крупной обработки. Для этого используют обычные калибры, индикаторы и микрометры — без них никто не выпускает продукцию к следующему мастеру.
- Параметры сборки тоже проходят свой контроль — чтобы ничего не перекосилось и не свистело после запуска. Если деталь не влезла в посадочное место — сразу на пересборку или «на доводку».
- Операторы и технологи отмечают результаты замеров прямо в маршрутных листах или в электронной системе MES, если производство более продвинутое.
В современных цехах часто используют автоматизированные системы — ошибки ловят прямо на линии, без участия человека. Например, сенсор сообщает о сбитых параметрах, и линия стопорится автоматически. Так не придётся потом разбирать уже собранные блоки.
В 2023 году завод «Кирово-Чепецкий машиностроительный» внедрил такую систему — количество бракованных деталей после обработки снизилось на 15%. Меньше переделок — значит цепочка не встаёт и все довольны.
Самое главное: этот вид контроля качества — не про тотальный надзор, а про защищённость бизнеса и обычных работников. Все знают: если что-то пошло не так — заметят, помогут, подскажут. И быстрее пойдёт дело.
Вот что важно помнить для операционного контроля:
- Контролировать все ключевые параметры прямо в ходе операции (а не после всей партии!)
- Использовать простые и понятные инструменты контроля
- Вести запись замеров — бумажные или электронные, но без самодеятельности
- Не экономить время на проверках — потраченное сейчас сэкономит нервы и деньги потом
Приемочный контроль: финальная точка
Вот он, последний барьер на пути брака к заказчику — приемочный контроль. Это, по сути, финальная проверка продукции перед отправкой клиенту. Если где-то что-то прозевали, тут уже исправить ничего нельзя: либо возвращаем в доработку, либо продукт уходит заказчику с гарантией качества.
В машиностроении такой этап особо важен: детали часто сложные и дорогие, да еще и работают в ответственных механизмах. Любой дефект — и весь станок может выйти из строя. По статистике Ассоциации инженеров-машиностроителей России, до 60% возвратов продукции по рекламациям связано как раз с недобросовестным приемочным контролем.
Суть процесса простая:
- Сверяют продукцию с требованиями ТУ или ГОСТ.
- Проверяют наличие сопроводительных документов.
- Делают визуальный и инструментальный контроль качества.
- Выбирают образцы для более подробных испытаний (случайная выборка).
На крупных заводах вся цепочка расписывается до мелочей и автоматизируется. Иногда используют статистический метод контроля: проверяют не каждую деталь, а только часть партии. Если вдруг найден брак — партия блокируется и идёт на повторную проверку.
«Эффективный приемочный контроль снижает количество скрытых дефектов в пять раз и экономит компании десятки миллионов рублей ежегодно», — отмечает Владимир Мельников, эксперт НПП "Машиностроитель".
Вот конкретные ошибки, которые попадаются чаще всего:
- Слабая проверка сертификатов и паспортов на детали.
- Использование не поверенных измерительных инструментов.
- Спешка из-за дедлайнов («и так сойдёт»).
Совет простой: не ленитесь проходить по чек-листу даже если на всё давит время. Лучше задержать отгрузку, чем потом ловить косяки и платить неустойки.
Кстати, если нужен реальный пример: именно при приемочном контроле на одном московском заводе сумели выявить ошибку в маркировке крепежа для железнодорожных вагонов. Если бы упустили — можно было бы получить не только убытки, но и крупные проблемы с безопасностью на транспорте.
Советы и лайфхаки: что работает на практике
Если хочется, чтобы контроль качества реально работал, а не превращался в скучную формальность, важно не забывать простые, но эффективные вещи.
- Не экономьте на инструментах. Крутая лазерная линейка или современный ультразвуковой дефектоскоп дешевле, чем потом переделывать всю партию.
- Не игнорируйте документацию. Даже если опытный мастер уверен на глаз, протоколируйте всё: кто мерял, чем мерял и что показало. Один раз забыли — потом не найдём, кто виноват, когда качество «улетит».
- Вводите понятные чек-листы. Даже если каждый в цеху считает себя экспертом, забыть одну мелочь просто. Простой чек-лист по операциям экономит время и нервы.
- Регулярно меняйте места и людей для инспекции. Если один и тот же мастер проверяет свою работу, ошибки пролетают на автомате. Лучше, когда чужой взгляд — сразу видно, где напортачили.
- Используйте цифровой контроль. Фото, видеозапись или простейшая база данных спасают от споров и путаницы. Можно быстро понять, где пошло что-то не так.
В крупных машиностроительных компаниях реально спасает внутренняя конкуренция между сменами. Например, на заводе «Электростанкомаш» внедрили таблицу с рейтингами: кто из бригад чаще ошибается и чья продукция меньше уходит в брак.
Бригада | Доля брака, % | Среднее время исправления, мин |
---|---|---|
Первая смена | 1,7 | 9 |
Вторая смена | 0,8 | 5 |
Не забывайте:
- Операционный контроль — не повод для штрафов, а страховка для всех.
- Краткие собрания раз в неделю помогают обнаружить типичные косяки — пусть даже за чашкой чая.
- Пусть каждый на линии не боится сказать о потенциальном браке. Если сотрудники молчат из страха, проблемы всплывут только в финале.
И самое простое: поощряйте тех, кто находит ошибки. Даже маленький бонус или простая похвала в рабочем чате делает чудеса с мотивацией.