Однажды я увидел, как огромный кусок дорогостоящей стали превращается в груду металлолома — просто потому что кто-то упустил момент контроля всего в одном сверлении. В мире машиностроения промашка может стоить миллионы — и это не преувеличение. Здесь каждый болт, каждая пластина и даже микроскопическая царапина имеют значение. Если хоть раз сталкивался с откровенно некачественными деталями — знаешь, к чему это приводит: к потере денег, срывам сроков, нервам и завалам склада неликвидом.
Зачем вообще нужен контроль в машиностроении
Контроль тут — не бюрократическая формальность. Всё просто: если детали не соответствуют чертежам, это никогда не пройдёт незамеченным, потому что на выходе такие машины или станки могут не только работать плохо, но и быть опасными. По статистике, крупнейшие аварии в машиностроительной отрасли в 90% случаев связаны с тем, что на каком-то этапе «пропустили» проверку. Все любят истории про неуловимые дефекты, найденные уже на сборке — но что делать, если сборка уже ушла заказчику? Представьте ситуацию: самолёт не может взлететь, потому что в одном из подшипников застряла вкрапинка металла размером с игольное ушко. Или, как однажды рассказывала мне Валентина, на скоростном поезде одна не проверенная деталь приводила к лишним вибрациям — и через год рельсы уходили в ремонт. Вот почему контроль — не про бумажки, а про реальную безопасность и надёжность.
Кстати, заводы КАМАЗа, АВТОВАЗа и Siemens публиковали свои методы контроля, и выяснилось: на их заводах — поэтапная, многоуровневая проверка. Обычно это минимум три барьера: сырьё, промежуточный этап, финальная инспекция. Иногда детали проходят до семи разных видов тестирования. А чего стоит неформальный опыт опытных контролёров, которые спустя годы на глаз отличают дефектные партии от годных ещё до микроскопа!
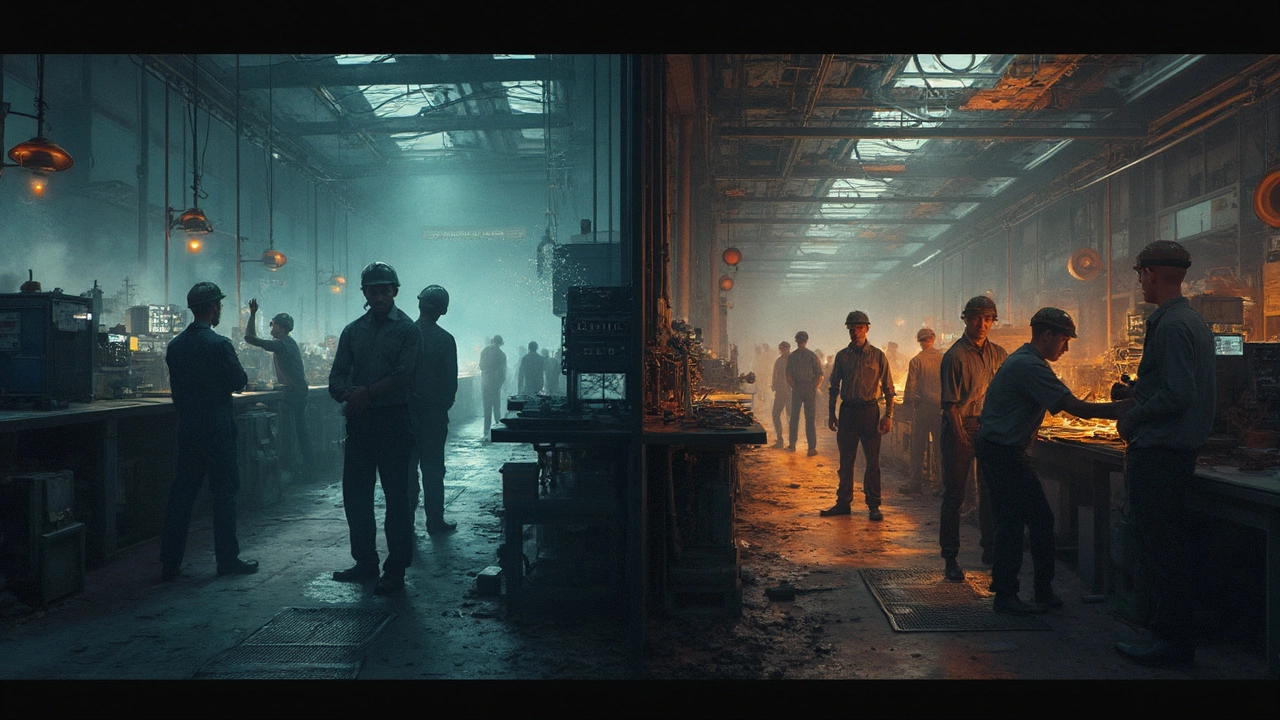
Виды контроля: как всё это устроено на деле
Контроль в машиностроении бывает разный: входной, операционный, выходной — звучит скучновато, но смысл прост. На входном этапе смотрят, не пришёл ли вместо легированной стали откровенное старьё. Нет смысла начинать производство, если сырьё не отвечает нужным стандартам ГОСТ и ТУ. По опыту, большие заводы заводят собственные лаборатории, чтобы тут же, на месте, проводить химический и физический анализ. Однажды инженер на «Уралмаше» рассказывал мне, как их лаборатория вычислила некачественный припой для сварки, который чуть не разложил партию насосных станций. После этого «глаз да глаз» за каждым грузовиком с металлом.
Операционный контроль — вот тут начинается магия. Во время обработки детали идут к контролёрам после каждой значимой фазы: токарная обработка, сверление, шлифовка, термообработка. Представь: рабочий с пылающим металлом только отошёл от стола, а к нему уже бегут с измерительным инструментом — штангенциркулем, микрометром, а иногда и с ультразвуком. На современных заводах пошёл тренд на автоматизацию: ставят камеры, лазеры, компьютерные системы моментального сканирования размеров и поверхностей. По факту — это борьба за минимальный процент брака. Современная статистика: на линии Hyundai за год количество дефектных деталей уменьшили с 5% до 0,2% после установки автоматических проверочных станций.
Про выходной контроль стоит поговорить отдельно. Это последняя преграда – когда изделие полностью готово, его тестируют в работе. Для некоторых моторов, коробок передач, редукторов устраивают суровые стендовые испытания: трясут, вибрируют, крутят в экстремальных режимах, чтобы вылезла малейшая ошибка. Если думаешь, что на этом можно расслабиться — ошибаешься. Бывали случаи, когда партии деталей отклоняли уже после упаковки, и приходилось разбирать продукцию обратно. Тут никуда не деться — единственный шанс гарантировать качество поставки. Контроль в машиностроении — это не только про технологию, а и про привычку проверять десять раз, прежде чем пустить вещь в дальнейшую жизнь.
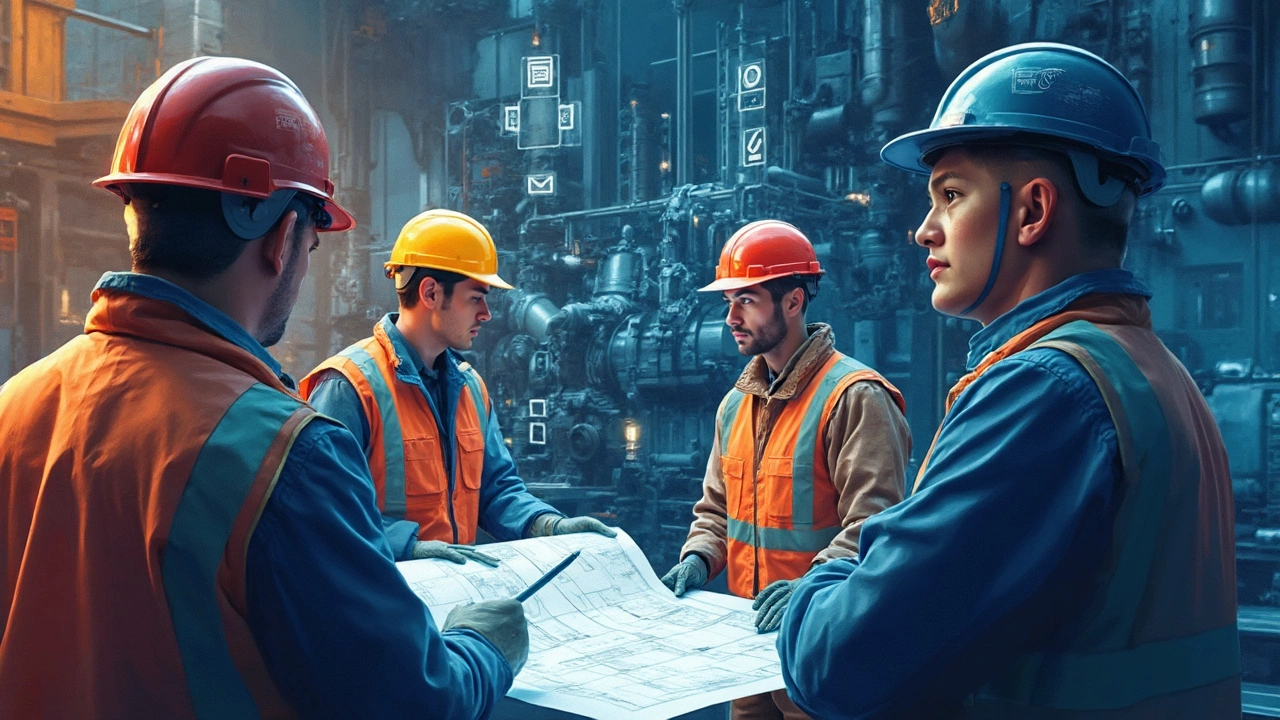
Чем опасен недостаточный контроль и как его усилить
Самое страшное не в том, что выпустишь брак, а в том, что не узнаешь об этом вовремя. Далеко ходить не надо — в 2018 году известный завод в Нижнем Новгороде понёс убытки на десятки миллионов из-за серии невыявленных дефектов. Дело было не в сырье, а в том, что отдел контроля «проскочил» ряд операций ради экономии времени. В итоге три крупных контракта расторгли, а уволенные специалисты долго искали новое место работы. Если контроль отсутствует или формальный, результат — рост затрат на ремонты, возвраты, репутационные скандалы.
Специалисты советуют: лучшая защита — это не слепая вера в опыт, а жёстко прописанные процедуры. Например, заводы Rolls-Royce не допускают к работе новых специалистов, пока те не пройдут минимум три месяца стажировки на линии контроля. На российском заводе «Салют» каждый контролёр имеет свой маршрут и не может покинуть линию без разрешения — чтобы никто не мог проскочить незамеченным. Самое полезное — вести электронные журналы: фиксировать обнаруженные проблемы, отмечать, на каком этапе «выстреливает» брак, анализировать и устранять первопричины.
По опыту — стоит внедрять принцип 4-х глаз: проверку одной детали делают независимо два человека или автомат и человек. Такой способ на практике снижает ошибки в два с лишним раза. Ещё полезны короткие ежедневные совещания отдела качества (даже на 10 минут): обсуждают текущие проблемы, планируют мини-проверки, договариваются, кого подключить к особым партиям. Регулярно обновлять регламенты — ни в коем случае не лениться прописывать новые случаи или инструкции. И не забывать о моральной стороне: контролёры должны чувствовать следствие своей работы. Как говорила мне Валентина, «если ты пропустишь дефект — завтра кто-то может пострадать из-за тебя».
Ещё интересный опыт есть у японцев: они называют свои регулярные мини-аудиты «кайзен» — улучшение через малые шаги. Каждый человек предлагает, как уменьшить риски ошибочного контроля. Там, где внедряли кайзен, уровень брака падает на треть уже за год. К слову, некоторые российские предприятия пересадили этот опыт, вынесли его на бумагу и в цифру — теперь новые контролёры учатся не только у наставников, но и по системе сценариев на планшетах. Меньше домашек, больше реальных примеров.
Контроль — якорь машиностроения. Здесь не про бюрократию, а про живое дело, результат которого отражается на каждом токаре, инженере, водителе, да и просто на безопасности родных. Хочешь уверенности в деталях — доверься контролю, и, как говорится в цеху: «сделай сейчас — меньше проблем потом».