Если кто-то думает, что цифровые технологии — это просто модная фишка для больших корпораций, он сильно ошибается. Сегодня без автоматизации и сбора данных даже средний завод рискует остаться позади. Конкуренты уже давно подключили системы мониторинга, учат роботов работать с людьми в одной команде и собирают аналитику о каждом этапе производственного процесса.
Зачем всё это? Во-первых, чтобы сократить простои и убрать ошибки, которые обычно возникают из-за человеческого фактора. Во-вторых, чтобы понимать, где теряются ресурсы и как можно производить больше с тем же или меньшим количеством сотрудников. Ну и, конечно, без цифры не получится быстро реагировать на новые заказы, меняющийся рынок или неожиданные поломки оборудования.
Самое интересное — доступ к цифровым платформам сейчас вполне реальный и для заводов среднего и даже малого бизнеса. Проводить цифровизацию можно поэтапно, не вкладывая сразу огромные суммы. И чем раньше начнёшь, тем быстрее увидишь результат: например, снижение издержек и рост качества продукции.
- Что меняют цифровые технологии в производстве
- Автоматизация: куда без неё сегодня
- Данные — главный помощник современного завода
- Экономия, качество и безопасность: три главных плюса
- Советы для быстрого старта с цифровыми решениями
Что меняют цифровые технологии в производстве
Раньше всё строилось на ручном труде и бумажных отчётах. Сегодня цифровые технологии сделали из цеха не просто цепочку станков, а современную площадку, где всё прозрачно и под контролем. Цифровизация — это уже не эксперимент, а рабочий инструмент для реальных задач.
Внедрение цифровых технологий позволяет видеть то, что раньше пропускали: можно в реальном времени отслеживать работу каждого оборудования, анализировать, где идёт перерасход материалов, а где сотрудники работают медленнее обычного. Например, на заводе «Калашников» после перехода на цифровую платформу выпуск брака снизился на 15%, а время простоя сократилось на четверть.
Отчёты больше не надо собирать вручную — всё формируется автоматически. Система сразу подаёт сигнал, если параметры отклоняются от нормы. Так успевают остановить выпуск брака ещё на этапе станка, а не после, когда материалы уже потрачены. Для сравнения, по данным НИИ автоматизации, свыше 60% предприятий после внедрения цифрового мониторинга отмечают экономию на закупках сырья и рост производительности.
Показатель | До внедрения цифры | После внедрения |
---|---|---|
Время простоя оборудования | 8-10 часов/месяц | 2-3 часа/месяц |
Уровень брака | до 7% | 2-3% |
Время реакции на поломку | 6 часов | 30-60 минут |
Цифровые решения делают производство гибче. Теперь можно быстро перестроить линии под новые задачи, добавить выпускаемый товар или оперативно внедрить новое ПО для оптимизации. Вот главные перемены, которые приносят цифровые технологии на завод:
- Отчёты и анализ без бумажной волокиты
- Своевременное выявление неполадок и простоев
- Прозрачное распределение ресурсов
- Понятная система оплаты по реально выполненной работе
- Возможность прогноза проблем по статистике прошлых лет
Проще говоря, появляется возможность управлять процессами не на глазок, а опираясь на цифры. Это экономит время, деньги и нервы.
Автоматизация: куда без неё сегодня
Автоматизация — не просто про роботов в цеху, которые двигают ящики. Это целая система инструментов, которая помогает избавиться от рутинных задач, ускорить процессы и снизить число ошибок. Например, автоматические линии сварки и сборки сегодня используют даже на небольших производствах. В России, по данным Ассоциации робототехники, количество промышленных роботов выросло вдвое за последние пять лет именно из-за доступности цифровых решений.
Самая простая выгода — экономия времени: если однотипную операцию теперь делает автомат, человеку можно доверить работу, где важны опыт и принятие решений. Ещё одна вещь — контроль качества. Машина не устанет и не пропустит дефект из-за усталости. Это особенно важно, если нужно держать чёткие стандарты, как на пищевых или фармацевтических предприятиях.
- Система ERP помогает следить за запасами и планировать закупки автоматически.
- IoT-датчики контролируют температуру, влажность, вибрацию и вовремя предупреждают о сбоях в оборудовании.
- Склады с автоматизированной системой обработки заказов резко уменьшают ошибки при подборе товаров.
Рынок труда тоже меняется: больше нужны специалисты, которые разбираются в цифровых технологиях и могут наладить или обслуживать современные системы. А базовые навыки работы с автоматизированным оборудованием становятся такими же обязательными, как умение читать чертежи. Без автоматизации среднего завода уже не получится быть конкурентоспособным на внутреннем или мировом рынке. И тут цифровые технологии — настоящий must-have для любого бизнеса.
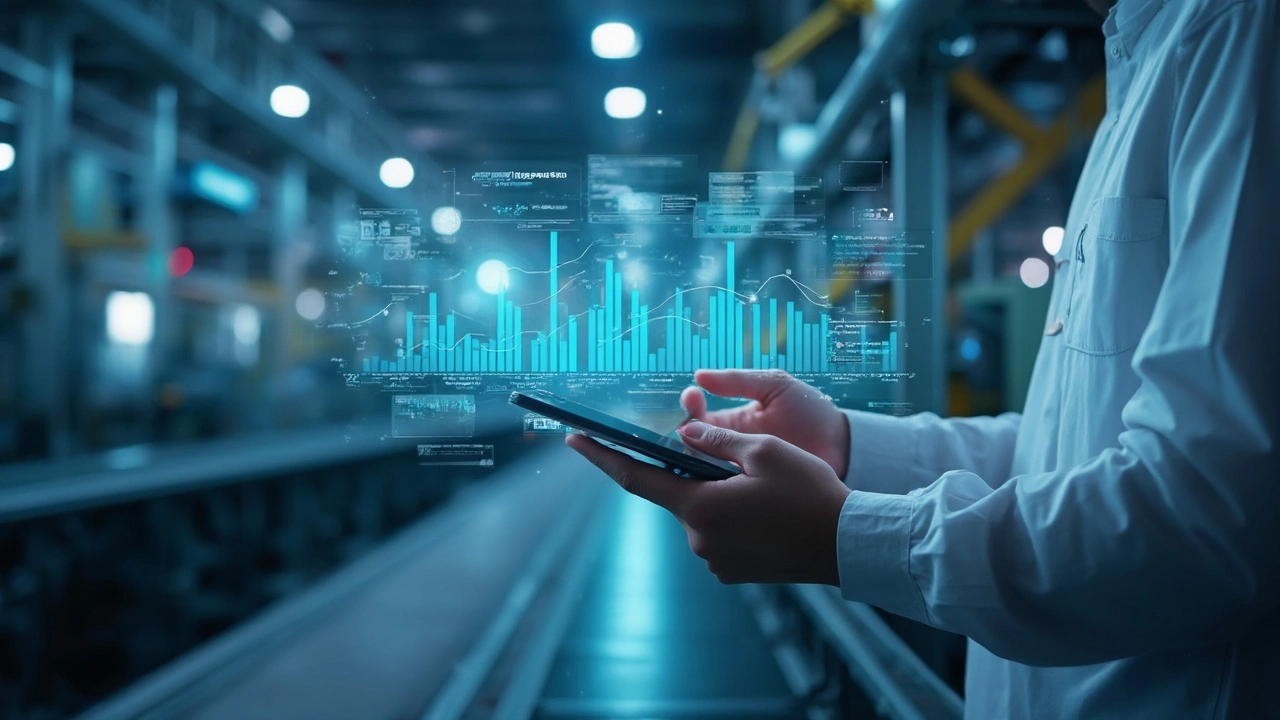
Данные — главный помощник современного завода
Данные — это не просто цифры из отчётов. На современном производстве они реально помогают зарабатывать больше и избегать неожиданных неприятностей. Сегодня почти каждый станок и даже светильники можно подключить к системе сбора данных. Всё это объединяется в одну сеть, и вы видите, где и что происходит прямо сейчас. Некоторые компании почти полностью ушли от бумажной отчётности: один сенсор передаёт в систему больше информации, чем раньше собирала целая смена.
Например, если на заводе стоит система сбора данных в реальном времени, про простой оборудования вы узнаете мгновенно. Сразу понятно, что сломалось и кого звать на ремонт. А ещё по этим же данным легко отследить, почему растут отходы или медленно идёт выпуск продукции.
- Данные показывают, где происходит частый брак.
- Позволяют сравнивать работу разных смен и участков.
- Помогают просчитать загрузку оборудования и не устраивать простои «на всякий случай».
- На их основе можно планировать ремонты, исходя из реального состояния техники, а не раз в год «по инструкции».
Реальный кейс: один завод внедрил систему анализа данных и смог за полгода снизить количество аварийных остановок на 35%. Ещё одна компания увидела, что одна станция даёт больше отходов из-за устаревших деталей, и после замены резко увеличила выход годной продукции.
Показатель | До цифровизации | После внедрения систем |
---|---|---|
Время простоя оборудования (ч/мес) | 35 | 17 |
Процент брака | 8% | 4,2% |
Число аварийных ремонтов | 12 | 7 |
При этом для работы с цифровыми данными не нужно сразу строить отдельную IT-команду. Сегодня на рынке полно готовых решений, которые быстро интегрируются даже в старые производственные линии. Главное — начать фиксировать данные и использовать их для принятия решений, а не просто складывать на сервере.
Всё это показывает: цифровые технологии делают работу завода значительно эффективнее. Данные — инструмент, который сразу даёт видимый результат. Чем чётче вы их получаете, тем проще экономить и управлять любым производством: от цеха до огромного промышленного комплекса.
Экономия, качество и безопасность: три главных плюса
Просчеты, брак и травмы — вот классические головные боли производства. Цифровые решения реально вмешиваются во все эти процессы и делают ситуацию проще и выгоднее.
Экономия начинается с автоматизации рутинных задач. Например, датчики и системы учёта теперь сами собирают данные о расходах энергии и материалов. Раньше на это уходили часы ручной работы, а сейчас один отчёт формируется за минуту и без ошибок. Например, заводы, внедрившие мониторинг электроэнергии, иногда экономят до 10% энергозатрат уже в первый год.
С качеством та же история. Человеческий фактор уходит на второй план, ведь цифровые технологии контролируют каждый этап: от закупки деталей до упаковки готового изделия. Камеры и датчики сразу отмечают дефекты, чтобы их исправили тут же, а не когда товар уже отправлен клиенту. На одном промышленном предприятии после внедрения такой системы количество возвратов снизилось в три раза.
Безопасность тоже стала технической задачей. Там, где раньше полагались на инструктаж и «авось», теперь ставят датчики газа, температуры, движения. Если где-то риск загореться или случиться аварии — система сразу подаст сигнал. К тому же управление механизмами все чаще происходит дистанционно, что снижает вероятность травм для персонала.
- Цифровые технологии помогают вести системную работу, а не надеяться на опыт одного мастера.
- Экономия достигается быстро за счет прозрачности ресурсов и оптимизации процессов.
- Качество растет стабильно, ведь компьютер видит то, что пропустит даже опытный сотрудник.
- Безопасность теперь зависит не только от правил, но и от точных алгоритмов и автоматизированных датчиков.
Все эти плюсы вскоре перестают быть преимуществом и становятся стандартом рынка. Кто не внедрит их сейчас, будет догонять завтра.
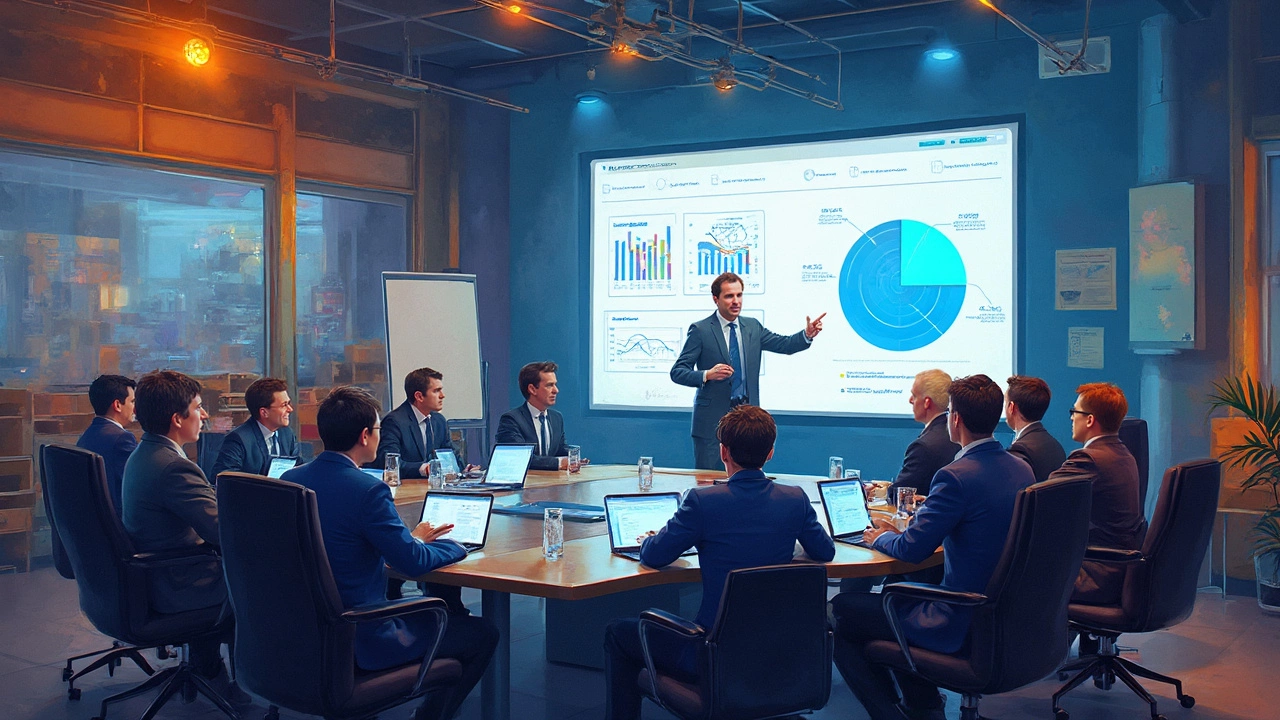
Советы для быстрого старта с цифровыми решениями
Первое, что тормозит большинство предприятий, — страх перед неизвестным. Многие думают, что внедрение цифровых технологий обернётся кучей проблем. На самом деле, чтобы начать, не нужен огромный бюджет или долгие согласования. Главное — не хвататься сразу за всё, а двигаться поэтапно и понимать свои реальные задачи.
- Цифровые технологии лучше внедрять с простых вещей: подключите мониторы для контроля температуры, датчики на оборудование, начните собирать базовые данные по простоям.
- В ходе пилотного проекта определите, где вы теряете больше всего времени и денег. Зачастую именно в этих местах внедрение технологий даёт самый быстрый экономический эффект.
- Не надо изобретать велосипед: используйте готовые решения, которые уже работают на заводах вашего масштаба. Например, системы мониторинга от «СтанкоПрома» или московское ПО «СКАД» прекрасно адаптируются к большинству российских производств.
- Чётко обозначьте, кто в команде отвечает за цифровизацию. Без ответственного всё быстро скатится в разговоры без дела.
- Первые успехи фиксируйте и используйте как аргумент для расширения масштаба — руководству всегда нужны конкретные цифры.
Вот пример простых этапов внедрения:
- Поставьте датчики на самое важное оборудование.
- Обучите персонал пользоваться новой системой: это могут быть даже короткие видеоуроки на планшете в цеху.
- Следите за данными в реальном времени, выявляйте узкие места и сразу устраняйте их.
- Расширяйте систему на другие участки, опираясь на первые полученные результаты.
Для тех, кто не верит в быстрый эффект, приведу свежие цифры. В 2024 году, по данным Минпромторга, российские компании, которые начали цифровизацию с малого пилотного участка, снизили просто до 32% уже в первый год.
Этап внедрения | Тип результата | Средний % повышения |
---|---|---|
Мониторинг оборудования | Снижение простоев | 31% |
Переход на электронный документооборот | Скорость обработки заказов | 25% |
Внедрение автоматического анализа брака | Снижение % дефектов | 20% |
И последний совет: советуйтесь с другими заводами — их опыт часто помогает избежать глупых ошибок. У производителей уже сложились свои клубы обмена опытом, не стесняйтесь к ним подключаться. Экономия времени и денег — это главное, а не «красивые» презентации.