В машиностроении качество — не просто абстрактный термин. Это фундаментальное требование, от которого зависят безопасность, надежность и, в конечном итоге, успех продукции на рынке. Чтобы обеспечить высокий уровень контроля качества, мы используем стратегию четырех «С»: согласованность, стабильность, стандартизация и систематизация.
Начнем с согласованности процессов. Это означает, что каждый этап производства должен быть упорядочен и координирован с другими, чтобы минимизировать ошибки. Представьте, что каждый работник — это музыкант в оркестре, где согласованность ведет к созданию гармоничной симфонии, а не хаоса. Как этого достичь? Возьмем простые меры — установление четких процедур и регулярная проверка их выполнения.
- Согласованность процессов
- Стабильность производства
- Стандартизация
- Систематизация
- Примеры из практики
Согласованность процессов
Согласованность — это ключевой элемент в контроле качества, особенно в машиностроении. Без хорошо согласованных процессов можно забыть о надежности и эффективности производства. Цель — добиться того, чтобы каждый этап работы был связан с предыдущими и последующими без сбоев и задержек.
Почему согласованность важна?
В крупных производственных цехах процесс сборки сложных машин можно сравнить с часовым механизмом, где каждая шестеренка должна находиться на своём месте. Без согласованности возникает риск нестыковок, из-за которых готовая продукция может выйти с дефектами. Это, в свою очередь, приводит к снижению качества и увеличению количества брака.
Как добиться согласованности?
Существуют проверенные способы, которые помогают наладить эффективное взаимодействие между процессами:
- Четкие инструкции и обучение: Каждый сотрудник должен знать, что и как делать. Периодические тренинги и обновления инструкций помогут держать всех в курсе.
- Автоматизация и цифровые технологии: Использование программного обеспечения для управления производственными процессами позволяет синхронизировать все этапы технологической цепочки в режиме реального времени.
- Кросс-функциональные команды: Небольшие группы, включающие специалистов из разных подразделений, помогают улучшать взаимодействие и решать проблемы на стыке процессов.
Пример из жизни
Один крупный автопроизводитель внедрил систему управления качеством, которая сократила количество ошибок на 20% за первый год. Они внимательно пересмотрели все места возможных сбоев между этапами и добавили автоматические индикаторы, указывающие на отклонения от нормы.
Год | Количество ошибок |
---|---|
2023 | 1000 |
2024 | 800 |
Эти примеры доказывают, что согласованность — это не просто формальность, а действенный инструмент повышения качества и надежности продукции. Поэтому важно не пренебрегать этим аспектом, а регулярно его пересматривать и улучшать.
Стабильность производства
Стабильность производства — это основа контроля качества в машиностроении. Без нее трудно предсказать, какой результат получится на выходе, и, как следствие, обеспечить надежность продукции.
Почему стабильность важна?
В условиях нестабильного производства количество брака может увеличиваться, что приводит к увеличению издержек и снижению конкурентоспособности. Это как готовить одно и то же блюдо, но каждый раз делать это на «глазок» — результат непредсказуем.
Как достичь стабильности?
- Контроль параметров оборудования: Регулярная калибровка оборудования позволяет избежать отклонений в процессе производства и уменьшает число возможных проблем.
- Мониторинг ключевых показателей: Например, анализ времени цикла и измерение температуры и давления помогают выявлять потенциальные сбои заранее.
- Обучение персонала: Регулярное обучение сотрудников новым методам и технологиям улучшает их квалификацию и навыки, что положительно сказывается на стабильности работы.
Интересный факт: Исследование, проведенное MIT в 2022 году, показало, что компании, инвестирующие в поддержание стабильности, снижают производственные издержки на 15% в долгосрочной перспективе.
Таким образом, в управлении качеством стабильность играет ключевую роль. И чем она выше, тем меньше вероятность появления проблем и сбоев в производственном процессе.
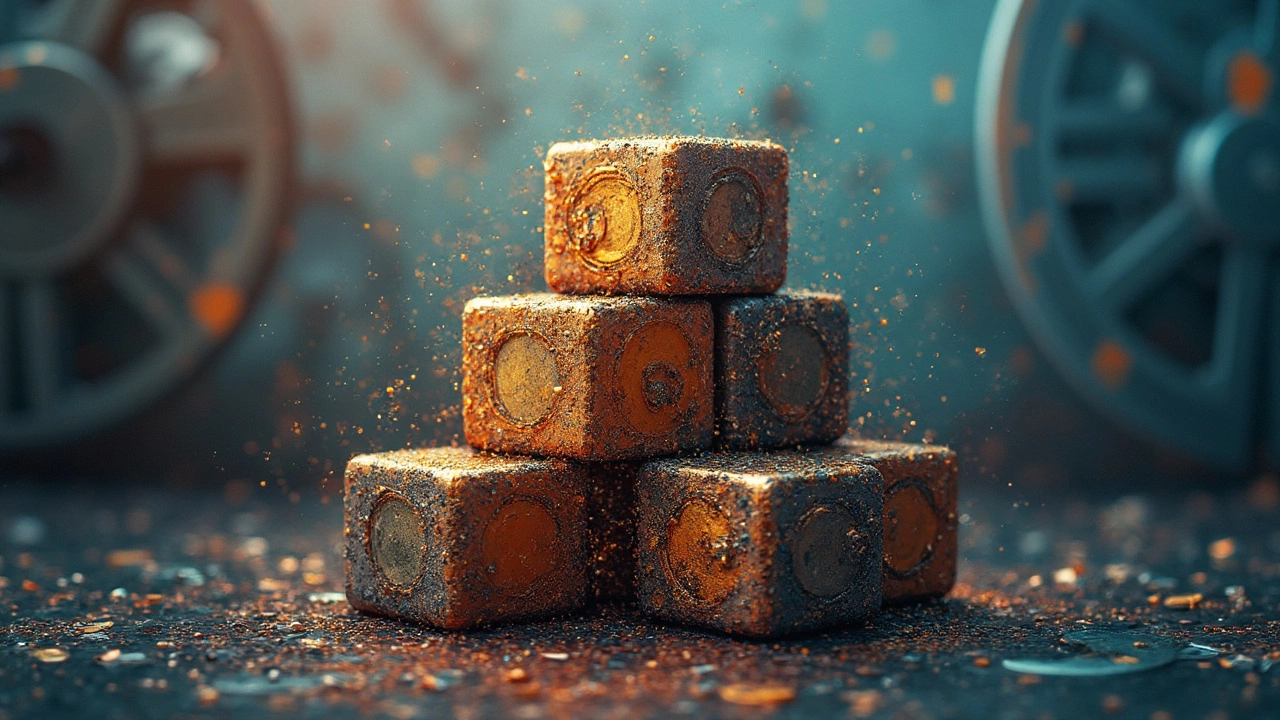
Стандартизация
Когда речь идет о машиностроении, стандартизация играет ключевую роль в поддержании качества на должном уровне. Без стандартизации процессы были бы хаотичными, что могло бы приводить к непредсказуемым результатам и снижению производительности.
Стандартизация предполагает установление единых правил и норм, которым должны следовать все на предприятии. Это как навигация по карте: без нее можно заблудиться и не дойти до цели.
Преимущества стандартизации
Во-первых, стандартизация сокращает сроки обучения новых сотрудников, потому что все процессы задокументированы и понятны. Во-вторых, она позволяет легче выявлять ошибки и быстро их исправлять. Например, если вы замечаете, что определенный процесс регулярно приводит к браку, можете пересмотреть и корректировать именно этот элемент, а не всё производство.
Реальные примеры
Рассмотрим компанию Toyota, которая внедрила стандартизацию в рамках своей системы бережливого производства. Это позволило значительно повысить эффективность и уменьшить количество дефектов в продукции. В результате, их автомобили считаются одними из самых надежных в мире.
Как внедрить стандарты?
- Первый шаг — написать подробные инструкции для каждого производственного этапа.
- Второй шаг — обеспечить доступ всех сотрудников к этим инструкциям.
- Третий шаг — регулярно проверять и обновлять стандарты в соответствии с инновациями и изменениями в производстве.
Хотя это может показаться сложной задачей, стандартизация приносит значительные преимущества, делая производство предсказуемым и надежным. Не стоит забывать, что стандарты должны быть гибкими, чтобы адаптироваться к новым вызовам и технологиям, таким как 3D печать и автоматизация процессов.
Систематизация
Систематизация — это основа, на которой строится успешный контроль качества. Как часто вам приходилось наблюдать хаос из-за отсутствия четкой структуры? В машиностроении наличие системы гарантирует упорядоченность и последовательность действий, что жизненно необходимо для высоких стандартов качества.
Почему систематизация важна?
Систематизация помогает минимизировать ошибки и недоразумения. Во время разработки новых моделей техники все детали процессов должны быть тщательно документированы и проверены. Без этой структуры даже самые опытные инженеры могут столкнуться с проблемами.
Согласно исследованиям компании «Эффективные решения», систематизация процессов снижает вероятность дефектов в производстве на 25%.
Как внедрить систематизацию в производственные процессы?
- Документация всех этапов: Каждая операция должна иметь четкие инструкции и стандарты выполнения.
- Обучение персонала: Регулярные тренинги и повышение квалификации помогут сохранить высокий уровень выполнения заданий.
- Интеграция технологий: Используйте современные ERP системы для слежения за процессами в реальном времени.
Для примера, посмотрим на компанию «TechnoEngines», которая применила систематизацию для контроля качества. Они внедрили автоматизированные системы проверки и отчетности, что позволило им сократить количество дефектов на 30% в течение первого года.
Отличная систематизация — это не просто бумага на столе, а действенный инструмент достижения непрерывного улучшения в производстве.
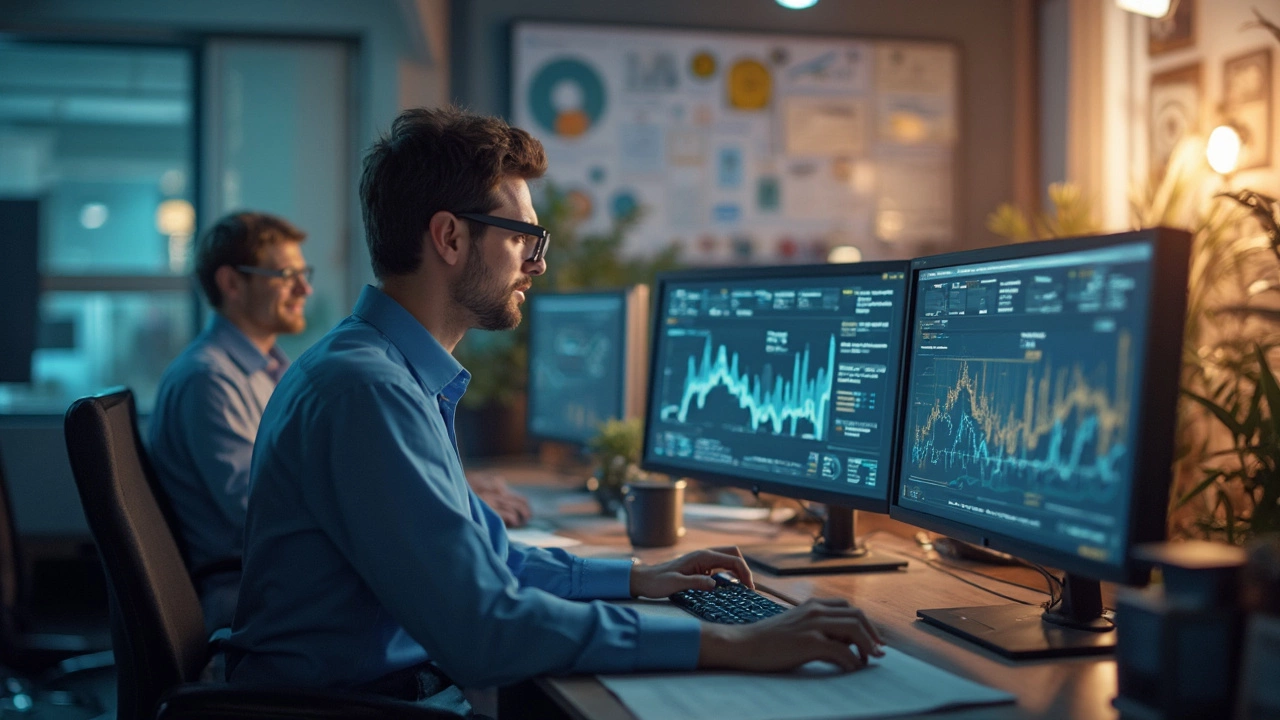
Примеры из практики
Рассмотрим, как компании применяют принципы четырех «С» в реальных условиях. На примере известной машиностроительной компании General Electric (GE), видно, как стандартизация играет ключевую роль в их производственном процессе. Они внедрили унифицированные процедуры для всей линии продукции, что позволило сократить временные затраты на оценку качества на 20%.
В 2023 году GE запустили инициативу под названием «Lean Manufacturing», в которой они фокусировались на согласованности и стабильности. Это привело к снижению процентного количества дефектов на 15% всего за год. Как говорил Томас Питерс, специалист по производственным процессам:
«Стремление к согласию и стабильности — это путь к совершенству. Это основы прочного производства.»
Систематизация как инструмент успеха
Другой яркий пример — компания Toyota. Они создали известную во всем мире систему «Toyota Production System», которая обобщает все четыре «С». Именно систематизация процессов производства позволила компании достичь высокой репутации в доставке качественной продукции в срок.
Они внедрили методику «Just In Time», что сделало их производство более гибким и адаптируемым к изменениям спроса. Систематизация процессов также значительно сократила время на переналадку линий.
Компания | Принцип | Результат |
---|---|---|
GE | Стандартизация | На 20% быстрее оценки по качеству |
GE | Согласованность и стабильность | На 15% меньше дефектов |
Toyota | Систематизация | Ускорение времени переналадки |
Эти примеры говорят сами за себя: повышение эффективности в контроле качества — это не миф, а результат четко выстроенных процессов и командной работы. Исполнение этих принципов ведет к более надежной и качественной продукции, удовлетворяющей потребности клиентов и повышающей конкурентоспособность компании.