Качество в машиностроении — не просто красивое слово или маркетинговый ход, а насущная необходимость для предприятий, стремящихся к успеху. Оно выходит далеко за пределы простой сборки деталей, охватывая науку и искусство создания продукта, который не подведет своего владельца.
Эта статья посвящена четырем основным аспектам, которые формируют основу для управления качеством в машиностроении. Каждая из них важна сама по себе, но в совокупности они создают мощную стратегию, позволяющую компаниям достигать и поддерживать высокий уровень качества продукции.
Понимание этих аспектов не только способствует повышению эффективности производства, но и укрепляет доверие к бренду, создавая больше возможностей для развития. Давайте разбираться в этом детально.
- Значение точной разработки
- Внедрение контроля качества на каждом этапе
- Интеграция процессов
- Постоянное улучшение качества
- Поддержка и обучение персонала
- Использование современных технологий
Значение точной разработки
Когда речь идет о управлении качеством в машиностроении, одно из первых слов, которое приходит на ум, — это «точность». На самом деле, точная разработка продукта является краеугольным камнем всего производственного процесса, начиная с самых первых чертежей и заканчивая окончательным изделием. В эпоху, когда технологии стремительно развиваются, даже малейшая неточность может привести к серьезным последствиям — от увеличения затрат до угрозы безопасности продукции.
Как показывает практика, недооценка значимости точности в разработке может вызвать целую цепочку проблем, начиная с перерасхода материалов и заканчивая несоответствием конечного продукта заданным стандартам и требованиям. Такие ошибки в итоге приводят к снижению эффективности производства, увеличению количества дефектов и даже к потере лояльности клиентов. Точный подход к разработке помогает избежать этих ловушек, что улучшает качество и надежность продукции, а также способствует росту конкурентоспособности на рынке.
Влияние точности на контроль качества
Каждое механическое изделие начинается с идеи и переходит в формат чертежа или цифровой модели. На этапе проектирования, где собирается огромное количество данных и учитываются разнообразные параметры, вопрос точности становится особенно актуальным. Именно на этом этапе закладываются основы для будущих процедур контроля качества. Если в разработке уже присутствуют элементы ошибок, они в дальнейшем смогут распространиться на все уровни производства, приводя к снижению уровня качества и увеличению затрат.
Известный инженер Генри Петроски однажды сказал: 'Точность не является средством достижения чего-либо, а в конечном итоге является целью производственного процесса'.
Рассмотрим пример, когда даже минимальные отклонения в проектировании машинного узла могут вызвать вибрацию, которая, в свою очередь, приведет к быстрой износе деталей. Это, в свою очередь, повлияет на производительность и долговечность оборудования, подрывая доверие к бренду. Точная разработка, напротив, обеспечивает безупречное функционирование каждой части машины, от самой простой детали до сложных механизмов. Это ключевой фактор, обеспечивающий долгосрочное качество продукции и удовлетворенность клиентов. Таким образом, точная разработка закладывает фундамент для успешного контроля качества на всех уровнях производства.
Внедрение контроля качества на каждом этапе
Контроль качества — это систематический процесс, который начинается с самого первого шага в проектировании и заканчивается только после выхода изделия на рынок. Важно заметить, что внедрение контроля качества на каждом этапе способствует не только выявлению возможных дефектов на ранних стадиях, но и позволяет снизить издержки и повысить удовлетворение клиентов. Такой подход дает возможность подойти к процессу производства с точностью хирурга: каждый элемент конструкции и функционала должен быть проверен.
Начнем с наиболее ранних этапов — проектирования и подготовки производства. На этом этапе усилия сосредоточены на проверке чертежей и прототипов. Организации, стремящиеся к совершенству, уделяют особое внимание применению методологии FMEA (Failure Mode and Effects Analysis), помогающей оценить потенциальные риски и дефекты еще на стадии планирования. Это позволяет предвидеть возможные слабые места и оперативно разрабатывать планы по их устранению.
"Совершенство достигается не тогда, когда нечего добавить, а тогда, когда нечего убрать." – Антуан де Сент-Экзюпери
Следующий важный этап — это производство. Здесь контроль качества включает в себя постоянный мониторинг и оценку каждого шага процесса. Специалисты используют разнообразные методы, такие как контрольные списки и технологические карты, которые помогают документировать и контролировать все аспекты процесса. Важно, чтобы специальное программное обеспечение и интеллектуальные системы были интегрированы для оперативного сбора данных и анализа их в режиме реального времени. Это обеспечивает быстрый отклик и помогает избежать крупных ошибок.
Завершающий этап — это тестирование готовой продукции. Здесь осуществляется проверка на соответствие заданным стандартам и техническим условиям. Автоматизированные системы и специальные установки позволяют проводить тесты, такие как испытания на прочность, устойчивость к износу и другие. Результаты неизменно документируются и анализируются, обеспечивая четкую обратную связь с предыдущими этапами и, при необходимости, внесение коррективов в процесс производства. Читателям стоит помнить статистику, что внедрение грамотных подходов к управлению качеством может снизить количество дефектов до 40%.
Не стоит забывать и об обратной связи с потребителями. Если изделие уже на рынке, важно учитывать мнения покупателей и их опыт использования продукта. Это позволяет не только исправить возможные ошибки, но и в дальнейшем разрабатывать новые модели на основе реальных данных. Такой подход укрепляет доверие к бренду и стимулирует инновации.
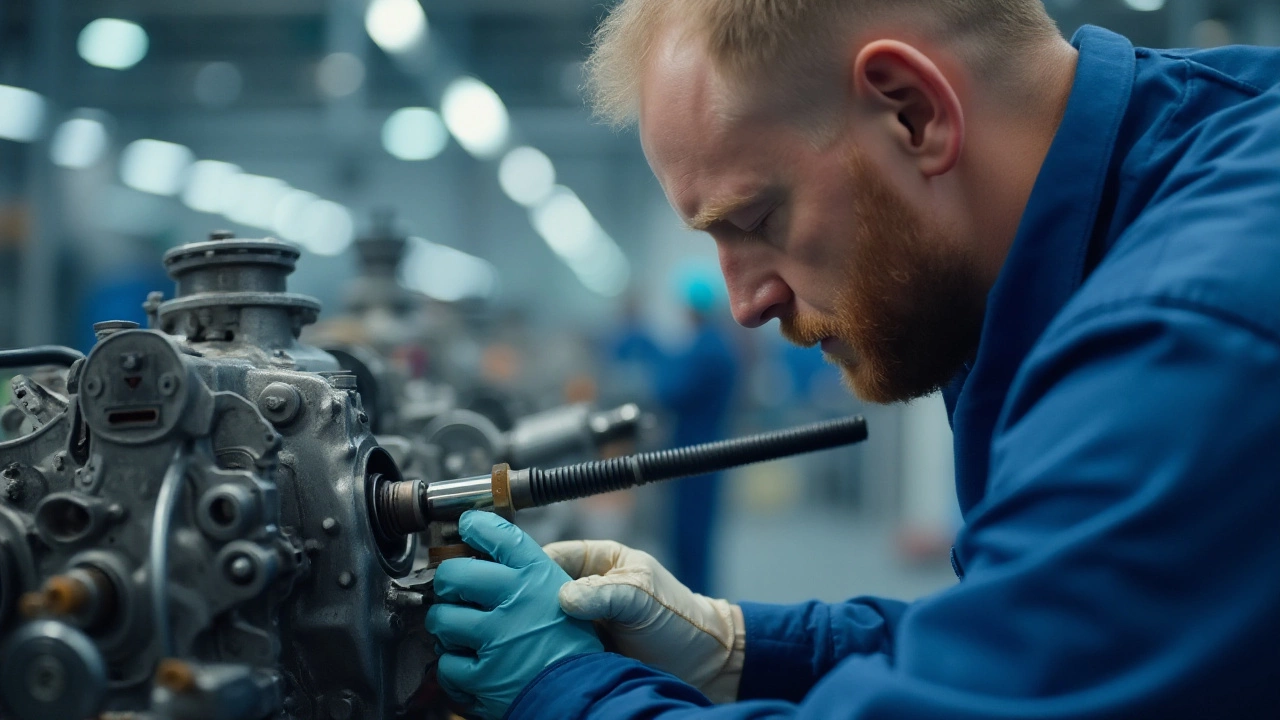
Интеграция процессов
В современном машиностроении интеграция процессов стала неотъемлемой частью стратегии любого преуспевающего предприятия. Она предполагает объединение всех этапов производства и управления в единый, слаженный механизм. Это помогает снизить издержки и повысить качество конечного продукта. Сегодня мы видим, что успешные компании строят свою работу на способности интегрировать, а не просто соединять процессы.
Чаще всего вопрос интеграции возникает на этапе проектирования. Это ключевой момент, когда инженеры и менеджеры должны тесно сотрудничать, чтобы продукт соответствовал ожиданиям потребителей. Интегрированная система управления позволяет мониторить каждую стадию — от проектирования до сборки. Это достигается благодаря комплексным программным решениям и взаимосвязанным информационным потокам. Этот подход помогает избежать ситуаций, когда разные отделы предприятия живут своей жизнью, не зная, что происходит за дверью соседа.
Важным аспектом интеграции является взаимопонимание и согласованность целей между всеми участниками процесса. Исследования показывают, что компании, внедрившие интеграционные стратегии, улучшили эффективность своих производственных линий на 20-30%. Внедрение системы контроля качества на всех уровнях производства делает возможным мгновенную идентификацию и устранение дефектов. Таким образом, минимизируется количество обратных процессов на исправление ошибок, что экономит время и ресурсы.
Один из пионеров в этой области, компания Toyota, ещё в XX веке внедрила так называемую систему «Точно вовремя». Она фокусируется на резком сокращении запасов и транспортировках, оптимизации процесса поставок. Такие методы способствовали формированию целого направления в теории управления производством, известного как 'бережливое производство', которое сейчас используется во всем мире. Именно благодаря интеграции процессов эта концепция показала высокую эффективность.
Интеграция процессов требует от компании системного подхода и готовности меняться. «Мы убеждены, что настоящая сила в способности адаптироваться и внедрять новые методы организации производства. Это позволяет нам быть лидерами в отрасли», — отмечает технологический директор одного из ведущих машиностроительных холдингов Европы.
Для успешной интеграции важным элементом является выбор правильных инструментов и технологий. Сегодня на рынке существует множество программного обеспечения, способного удовлетворить запросы даже самых требовательных клиентов. Однако ключ к успеху — это не просто использование технологий для интеграции, а их грамотное внедрение и адаптация под нужды конкретного предприятия. Новейшие достижения в области IoT и Big Data позволяют компаниям собирать и анализировать огромные массивы данных в реальном времени, тем самым открывая возможности для оптимизации каждого элемента производства.
Ошибочный путь — думать, что интеграция процессов — это разовый проект. В действительности этот процесс должен быть непрерывным. Только так можно достичь высокой стабильности в выпуске продукции и улучшать её со временем. В этом случае слова «качество», «эффективность» и «управление качеством» становятся не абстракцией, а естественной частью корпоративной культуры. Интеграция процессов — это не цель, а средство, которое помогает компаниям расти и достигать новых высот, как в производительности, так и в качестве их продуктов.
Постоянное улучшение качества
Когда речь заходит о постоянном улучшении качества в машиностроении, одно из первых, что приходит на ум, — это философия Kaizen, широко распространенная на заводах по всему миру. Эта философия акцентирует внимание на постепенных, но постоянных улучшениях, вовлекая весь персонал в процесс поиска решений и оптимизации. Воплощение этой идеи позволяет не только улучшать контроль качества, но и серьезно снижать издержки производства за счет уменьшения количества дефектов и неэффективных процессов.
Создается культура, в которой каждый сотрудник, будь то инженер, оператор станков или линейный менеджер, чувствует свою ответственность и вклад в общий успех. Такой подход стимулирует не только креативность, но и способствует формированию сплоченного коллектива, чей коллективный опыт используется для решения задач. Ключевым моментом является создание обратной связи между работниками и руководством. Это позволяет последнему видеть реальные проблемы, появляющиеся на различных уровнях производственного процесса.
Интересно отметить, что такие гиганты, как Toyota, делают акцент на малых улучшениях каждый день. Как-то Акио Тойода сказал:
"Мы стремимся дать нашим работникам свободу предлагать нововведения, и это делает наш успех устойчивым".Это стремление явно отразилось на подходе к разработке, который перешел в стандарт не только для автомобилей, но и для любых крупных продуктов.
Методы и инструменты для улучшения качества
На практике постоянное улучшение качества может включать как изменения в проектировании, так и улучшение процессов включая их интеграцию и автоматизацию. Распространенной практикой является использование методов, таких как шесть сигм (Six Sigma) или инструменты статистического анализа для выявления узких мест в производственных циклах. Эти методы позволяют не только количественно оценить проблему, но и предложить математически обоснованные решения.
Важным аспектом является обучение персонала новым методам и инструментам, что позволяет адаптироваться к изменениям и использовать их как на уровне производственного цеха, так и на уровнях управления. Это гарантирует, что все сотрудники располагают необходимыми знаниями и навыками для участия в процессе улучшения качества.
Модернизация оборудования, внедрение информационных систем для мониторинга и анализа процессов — все это способствует укреплению качества продукции и позволяет снизить процент брака. В условиях увеличения конкуренции на рынке, использование таких стратегий становится не просто дополнительным преимуществом, а необходимостью для сохранения лидерских позиций.
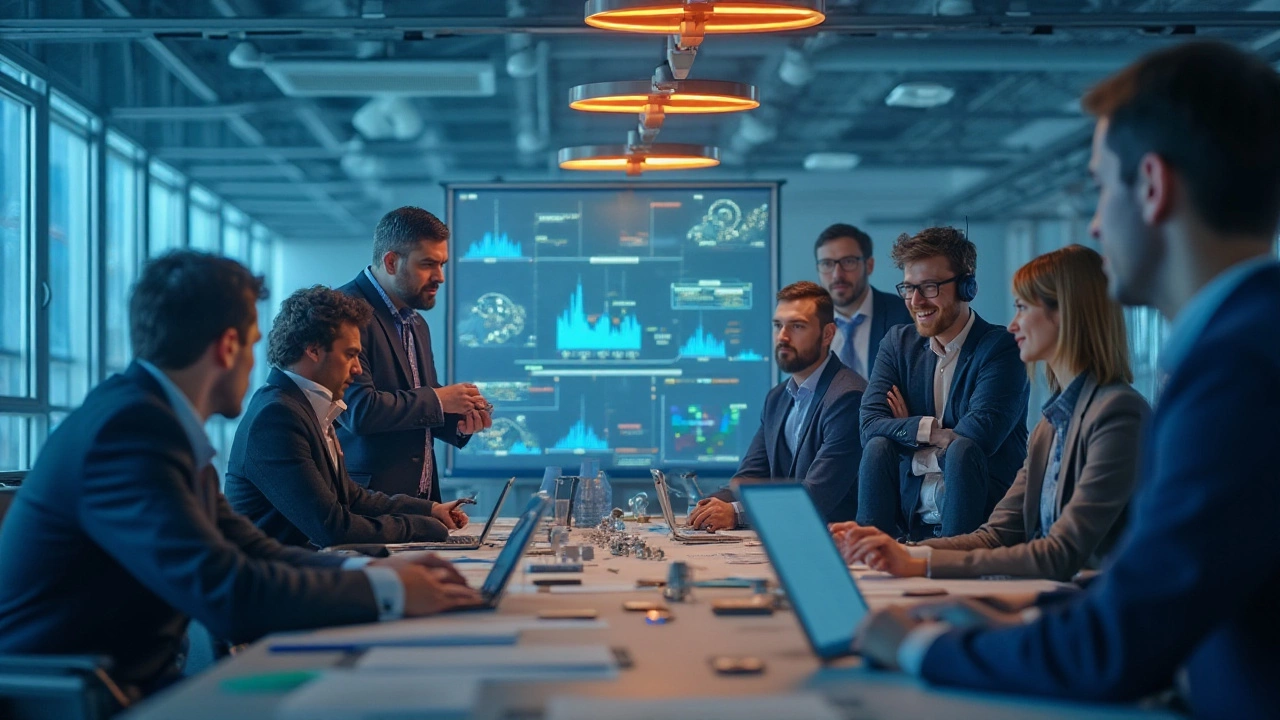
Поддержка и обучение персонала
Важность качественного обучения и поддержки персонала в области управления качеством в машиностроении трудно переоценить. Люди — это главный актив любой компании, и на них ложится ответственность за производство безупречных изделий. Особенно в такой сложной области, как машиностроение, где каждая ошибка может стоить значительных усилий и ресурсов. Поэтому опытные компании стремятся создать благоприятную среду для своих сотрудников, чтобы они могли обучаться и развиваться, привнося свою лепту в общий успех.
Одним из важных аспектов является организация регулярных курсов и тренингов, которые помогают сотрудникам оставаться в курсе последних достижений в области технологий и методов контроля качества. Обучение позволяет не только повысить профессиональные навыки, но и усилить понимание стратегий управления процессами. Когда человек знает, как и почему использует те или иные методы, он становится более уверенным и способен принимать более взвешенные решения.
"Лидеры рынка обычно тратят до 20% времени своих работников на обучение и развитие, что в долгосрочной перспективе приводит к снижению числа дефектов до 15%", — говорится в исследовании компании McKinsey.
Важная роль идет и на поддержание мотивации сотрудников. Здесь играет роль не только материальное поощрение, но и создание атмосферы, в которой человек чувствует себя частью команды, работающей на единый результат. Ведь довольный работник вкладывает больше души в свою работу, а это напрямую влияет на качество конечного продукта.
Использование современных технологий в обучении
В современном мире технологии стали неотъемлемой частью процесса обучения. Различные обучающие платформы, виртуальные симуляторы и онлайн-курсы значительно упрощают доступ к необходимой информации. В машиностроении такие инструменты позволяют воспроизвести реальные производственные ситуации, что дает возможность сотрудникам учиться на ошибках без риска для компании.
- Виртуальные симуляции помогают сотрудникам разобраться в сложных процессах на практике.
- Платформы для онлайн-обучения позволяют осваивать новые навыки в удобное время.
- Вебинары и видеолекции от экспертов в отрасли помогают расширить горизонты и вдохновить на инновации.
Эти подходы обеспечивают постоянное развитие и адаптацию к меняющимся условиям, что очень важно для повышения уровня эффективности производства.
Использование современных технологий
Современные технологии все больше проникают в управление качеством и трансформируют машиностроение до неузнаваемости. Начнем с того, что благодаря инновациям в области искусственного интеллекта (ИИ), автоматизации и интернета вещей (IoT), предприятия смогли значительно улучшить точность и эффективность своего производства. Например, искусственный интеллект помогает анализировать огромные объемы данных и предсказывать возможные сбои, что позволяет непрерывно поддерживать высокий уровень качества продукции. Это действительно произвело революцию в подходах к контролю качества, делая его более интеллектуальным и проактивным.
Технологии дополненной реальности (AR) также нашли свое место в машиностроении. Они используются для визуализации деталировки в реальном времени, помогая инженерам точно сопоставлять проектные данные с фактическими производственными. Это обеспечивает не только упрощение сложных процессов, но и существенное снижение ошибок при сборке сложных механизмов. Такие технологии позволяют не просто выполнять заказы, но и осваивать совершенно новые методики производства, которые без технологий были бы невозможны.
3D-печать — еще один ключевой компонент современного машиностроения. Она дает возможность создавать прототипы и конечные изделия с невероятной точностью и скоростью. Это становится особенно важным инструментом в создании уникальных деталей или небольших партий продукции, где традиционные методы просто неэффективны. «Технологическая революция создала условия для персонификации производства, когда каждая деталь может быть индивидуально адаптирована под нужды конкретного клиента», — отмечает Мирослав Копейкин, эксперт в области промышленного дизайна.
Не стоит забывать и о важности облачных технологий для контроля качества. Облачные системы обеспечивают централизованное хранение и доступ ко всей информации о качестве изделий, что делает ее доступной для анализа и быстрого реагирования в случае выявления дефектов. Это особенно важно для глобальных корпораций, продукция которых поставляется по всему миру и требует строгого ведения документации и контроля на всех этапах производства.
Интересно, что аналитики прогнозируют, что уже к 2025 году до 40% всех заводов интегрируют IoT устройства во все основные производственные процессы. Важно понимать, что эффективность производства, достигнутая благодаря технологиям, идет рука об руку с интеллектуальной обработкой данных и профессиональной подготовкой сотрудников. Благодаря этому, достигается главная цель — создание продукта, который удовлетворяет все запросы рынка и обеспечивает безопасность и удобство его использования. Это не только делает производство более конкурентоспособным, но и утверждает «новую норму», где качество продукции поддерживается на высочайшем уровне постоянно.